In the fast-paced development of industrial machinery, precision is not merely a beneficial attribute—it is essential. This precision is especially critical in the production of bearings, a core component whose quality can substantially impact the overall efficiency and performance of machinery. In this article, we will explore how precision bearings can enhance the performance of the machinery, diving into their impact on energy efficiency, performance standards, and ultimately, the cost-effectiveness of your operations.
The Impact of Industrial Bearings on Energy Efficiency
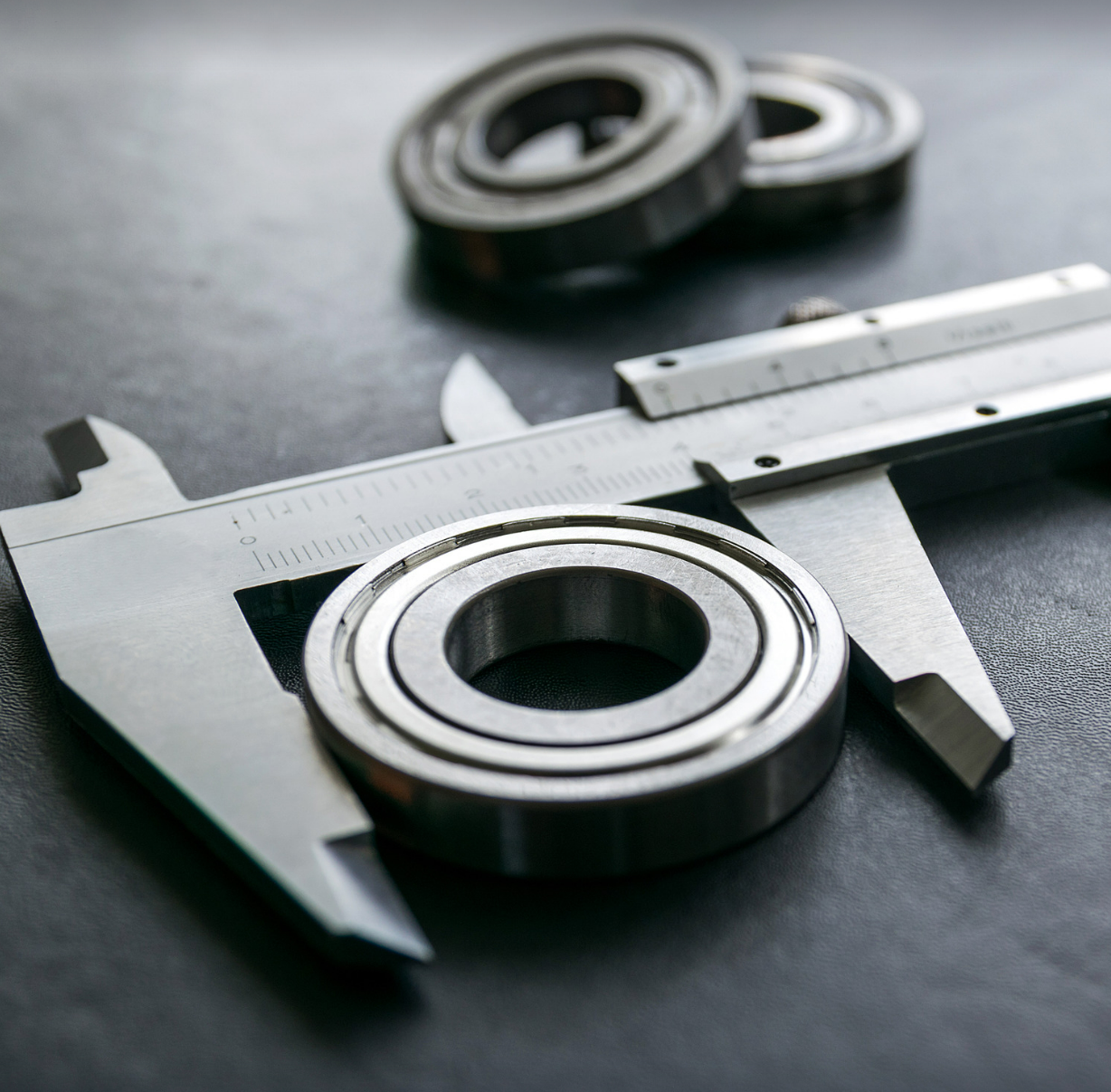
Precision Bearings: An Epitome of Performance
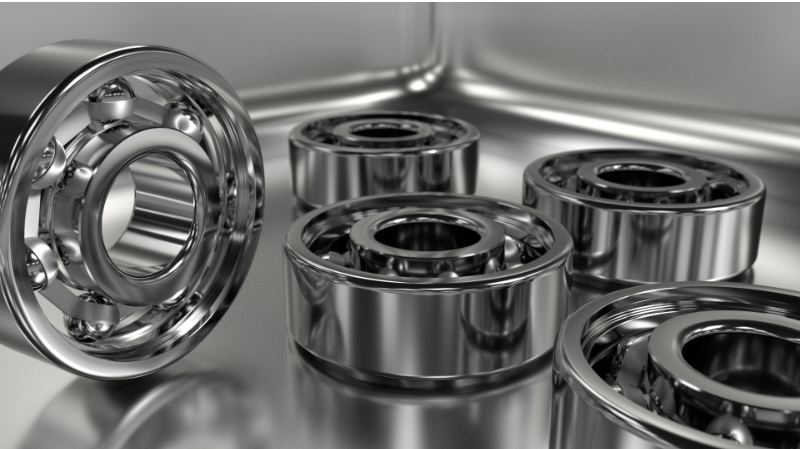
Adherence to Industry Standards
Precision bearings adhere to stringent industry standards and specifications, such as ISO standards for dimensional accuracy and ABEC ratings for tolerances. These standards ensure that the bearings meet the rigorous demands of various industrial bearings applications, fostering trust among manufacturers and ensuring compatibility and interchangeability across different systems. This adherence is not just about maintaining quality but also about ensuring that all parts of a mechanical system can work together seamlessly, thereby enhancing overall reliability and performance.
Innovation and Miniaturization
The relentless pursuit of precision in bearing manufacturing has not only improved existing machinery but has also paved the way for innovative advancements. For instance, the development of miniature bearings has revolutionized microelectronics, while high-speed bearings have pushed the limits in automotive and aerospace applications. As industries increasingly demand smaller, lighter, and more efficient solutions, precision bearings continue to play a critical role in enabling the miniaturization and optimization of mechanical systems.
Cost-Saving Advantages
Although precision bearings often come with a higher initial investment, the long-term benefits they offer far outweigh these initial costs. By reducing friction and wear and tear, and by extending maintenance intervals, precision bearings provide substantial cost savings throughout their lifespan. Furthermore, their superior performance and reliability mean fewer downtimes, increased productivity, and enhanced profitability for businesses across various sectors.
Consistency and Quality in Manufacturing
In the competitive landscape of manufacturing, consistency and quality are paramount. Precision bearings help uphold these standards by delivering uniform performance and tight tolerances. Whether it’s in consumer electronics or heavy machinery, using precision bearings ensures that every product consistently meets or exceeds customer expectations, fostering brand trust and loyalty.
- Difference between a precision bearing and a standard bearing: Precision bearings are manufactured to tighter tolerances and higher standards of accuracy than standard bearings, leading to superior performance, reliability, and consistency.
- Role of precision bearings in manufacturing processes: They provide stable support, smooth rotation, and minimal friction, enhancing the efficiency, productivity, and quality of manufacturing equipment.
- Precision bearings improve the lifespan of machinery: Precision bearings improve machinery lifespan by reducing wear and tear, minimizing maintenance needs, and enhancing overall reliability and performance.
- Precision bearings enhance the performance of industrial equipment: They reduce friction, vibration, and heat generation, leading to smoother operations, higher efficiency, and improved productivity, which, in turn, boosts machinery performance.
- Advancements in precision bearing manufacturing: Advancements include improvements in materials, surface treatments, lubrication techniques, and manufacturing processes, which have resulted in bearings that offer higher precision, durability, and reliability.
- Precision bearings contribute to overall machinery efficiency: They minimize energy loss due to friction, optimize rotational motion, and ensure precise alignment in machinery, enhancing overall efficiency, reducing operational costs, and maximizing productivity. Precision bearings are not just components; they are foundational elements that drive the efficiency and reliability of modern machinery. Investing in the right precision bearings is not merely a choice but a strategic decision that can significantly enhance the performance and profitability of industrial bearings operations.
Conclusion
The adoption of precision bearings is essential for any industry looking to enhance the performance, reliability, and energy efficiency of their machinery. For those seeking top-quality precision bearings, KG India stands out as a prime supplier. KG India offers a diverse range of precision bearings that meet rigorous international standards, ensuring optimal performance for various industrial applications.
Whether you are involved in automotive, aerospace, manufacturing, or any sector requiring high-standard components, KG India provides precision bearings that can dramatically improve the efficiency and lifespan of your machinery. By integrating precision bearings by KG India into your equipment, you can expect reduced maintenance costs, enhanced productivity, and superior overall performance.
For more detailed information on the specifications and availability of precision bearings, visit www.kgindia.co.in
Here, you can explore their extensive product range and learn how their solutions can be tailored to meet the unique needs of your business. Investing in precision bearings from KG India means investing in the future of your machinery’s performance.